Eco-conscious businesses along with consumers now actively choose sustainable alternatives as their packaging and carrying solutions in modern times. The non woven fabric carry bag has become highly popular because it presents both cost-effective solutions and durable properties alongside environmental sustainability characteristics. Have you ever considered the manufacturing steps involved in creating these products? barcelona packs dyeing into four main stages constructing basic woven textile fabrics as well as digital printing and finishing. The process of building these environmentally friendly bags is explored in detail in this article.
Step 1: Raw Material Selection Non Woven Fabric Carry Bag
Raw material selection determines the initial stage of making non woven fabric carry bags. Depending on their production method non woven fabric carry bags originate from polypropylene (PP) granules that become fibers through melting processes. Synthetic fibers merge through three distinct methods to form non woven fabric. Fiber bonding produces non woven fabrics because they lack woven fabric’s interlocking threads structure.
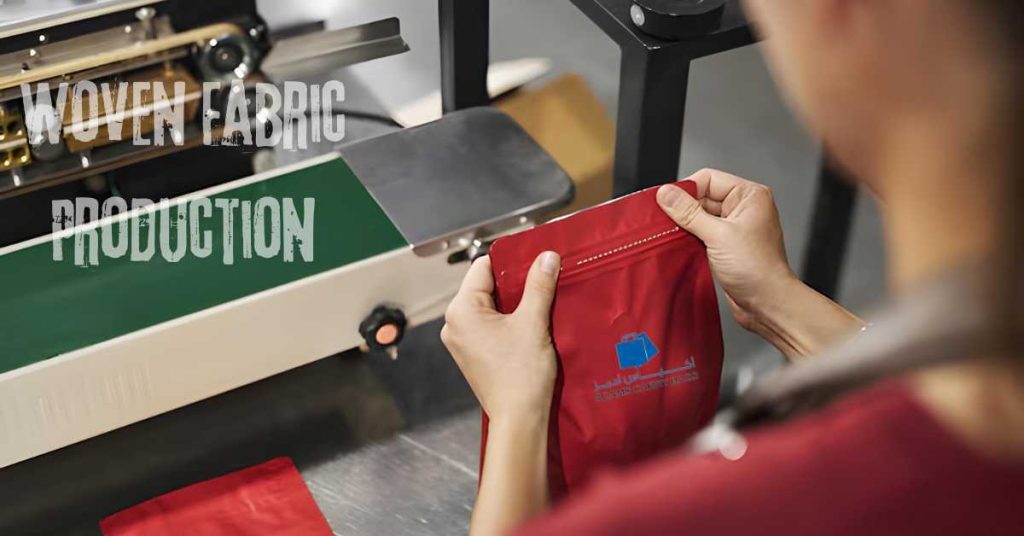
Step 2: Non Woven Fabric Production
The next production phase begins following raw material selection. The non woven fabric is created using one of the following techniques:
Spunbond Technology: Spunbond technology represents the prevalent manufacturing process for non woven fabric. The production of continuous filaments occurs when polypropylene granules melt while moving through miniature nozzles. A random arrangement of these filaments happens on a conveyor belt until heat and pressure bonds them together.
Meltblown Technology: The production method starts with melting polymers and distributing them into thin filaments through high-volume hot-air streams. Meltblown fabric finds use in filtration applications yetamaximizes strength through combinations with spunbond layers.
The production process ends with large diameter rolls of fabric before advancing to future manufacturing stages.
Step 3: Cutting and Shaping
Manufacturers first generate non woven fabric which they then cut into specific pieces to match their personalized bag preferences. Thanks to advanced die-cutting machines production achieves greater accuracy in measurements so it becomes simpler to maintain uniformity throughout manufacturing. The bags come in various shapes and sizes, including:
- D-cut bags
- W-cut bags
- Box bags
- Handle bags
Step 4: Printing and Customization
Non woven fabric carry bags gain appeal from their promotional feature which allows customers to add company branding and marketing messages. Printing techniques used in this stage include:
Screen Printing: Ideal for simple designs and short-run productions.
Flexographic Printing: The fabric receives its ink layers through the application of elastic rubber plates.
Offset Printing: The printing process continues to deliver professional quality solutions that scale up for industrial manufacturing.
Heat Transfer Printing: Best for detailed and colorful graphics.
Business organizations that use non woven fabric carry bags need to perform printing as an essential step for their promotional activities.
Step 5: Stitching and Sealing
After fabric cutting and printing operations the bag assembly process starts. There are two primary methods for bag assembly:
Stitching: Sewing machines perform two functions to make the bag stronger by joining handles and edges together.
Ultrasonic Sealing: A high-frequency sound energy system forms fabric bonds between layers without using thread or glue. The method delivers quick production results alongside outstanding seamless outcomes.
Step 6: Handle Attachment
Non woven fabric carry bags require handles to function as both functional accessories and supportive elements. The handles can be:
Die-cut handles: Pre-made opening gaps in theüpéé section of the bag exist.
Loop handles: The separate handles use the same non woven fabric for their construction.
Padded handles: Additional padding for extra comfort.
Step 7: Quality Control and Inspection
An extensive quality check happens to finished bags before they receive the packaging process and shipping stage. Inspectors verify:
- Print quality and alignment
- Stitching and sealing integrity
- Size accuracy
- Strength and durability
Packaging only begins after bags successfully pass quality tests.
Step 8: Packaging and Distribution
Testing concludes successfully and the non woven fabric carry bags move to folding before packaging and storage for distribution. Each bundle of non woven fabric carry bags includes a predefined number of items, according to standard factory specifications. Carry bags go from the production line to wholesalers and retailers or they reach end-customers.
Environmental Benefits of Non Woven Fabric Carry Bags
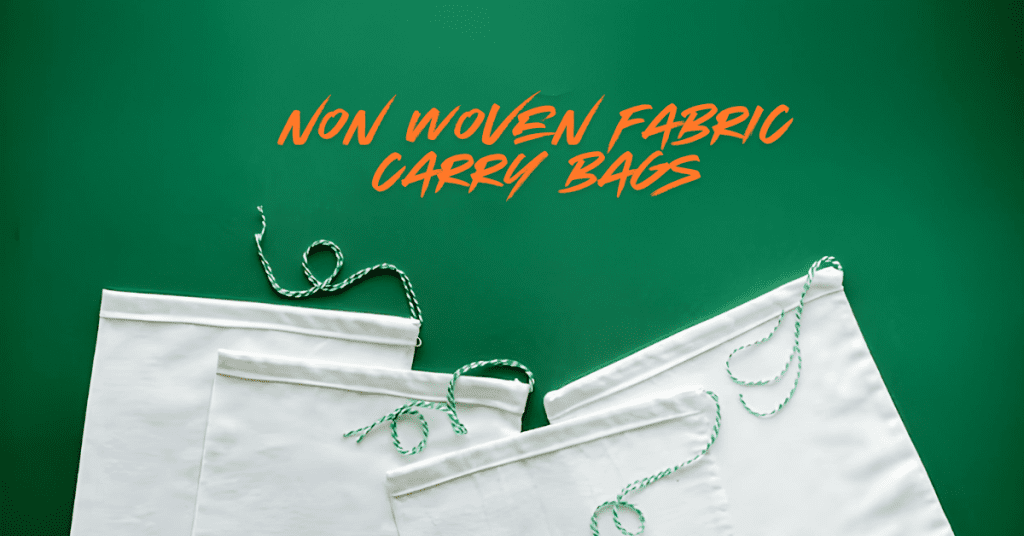
The market demand for non woven fabric carry bags continues increasing because of their environmentally friendly features. Some key benefits include:
Reusability: The bags function for numerous uses that minimizes the amount of throwaway plastic waste.
Biodegradability: Excavation of non woven fabric happens at a faster rate than traditional plastic bags.
Recyclability: This sustainable material allows reuse followed by reprocessing procedures.
Reduced Carbon Footprint: factory processes energy usage for fabric carry bags remains lower than it does for plastic bags.
Conclusion
Fabricating non woven fabric carry bags necessitates a thorough series of manufacturing operations that include choosing raw materials and conduct printing then perform cutting followed by stitching to complete quality control assessments. Non woven fabric carry bags serve as both an eco-friendly and fashionable substitute for standard plastic shopping bags. Non woven fabric carry bags will remain crucial to environmental impact reduction as consumers and businesses maximize their adoption of sustainable products. These reusable bags deliver both business branding opportunities and personal utility benefits as sustainable solutions for creating a better future environment